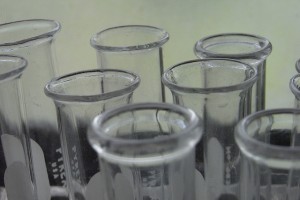
Bev was fed up. She was in the middle of working on her PhD thesis which relied on data from a large and ongoing animal study. When she went to the storage freezer to retrieve some samples for her analyses, she found nothing. Or rather, she found boxes upon boxes of samples… but not the ones she had been looking for.
The study, which was undertaken by a major university, had been going on for several years. The project and data managers had perfectly orchestrated the structure of the study, and things had been going well. They had a solid and time-tested plan for recruiting subjects. They networked between the project’s three sites and did everything necessary to keep the study productive and on track. They even organized the database into an incredibly efficient library system for processing data requests and loaning out data subsets. But even with all those careful strategies in place, there was one area which had become woefully neglected: the physical samples.
At one time, the storage freezers had been meticulously lined with many types of samples collected from the research participants – blood, plasma, and other biological specimens. Once collected, they were labeled, preserved, sorted by type, and placed into storage. In the early days, when samples were fewer and space plenty, it was easy to maintain order with a little planning and diligence. But over the years, as more participants were added to the study, the number of samples continued to grow – making available freezer space a more and more precious resource.
With a little restructuring of the inventory and some long term planning for the bio repository, this would not have been a major issue. However, the job of inventory management typically fell on the shoulders of younger, less-experienced researchers. Well-meaning and always eager to contribute, these organizers would come onto the project ready to care for the samples and ensure they found their proper places. The only problem was that these managers eventually did what they had come to the university to do: complete their work, graduate, and move on to studies and careers of their own.
As students came and went, so too did several styles of inventory organization. With a new student manager came a new method for organizing and storing samples. Boxes got shuffled from freezer to freezer, from shelf to shelf, and still the inventory grew. By the time Bev arrived on the scene, the study had amassed over 30,000 biological samples in over 1,000 freezer units across 3 different storage sites. The pieces were all there, but it was very difficult to visualize the complete puzzle. When the samples Bev had been looking for turned out to be exhausted and unrecoverable, she knew something had to be done.
After joining the inventory team, she began an assessment of the storage facilities. She convinced the project managers to hire a couple of assistants, and together they navigated the labyrinth of storage, shuffling through boxes and making notes of what samples had ended up where. At the end of a two month period, they had established a map of the freezers showing the location of various sample types.
Still Bev longed for a more efficient organization system – one that didn’t allow for surprises like misplaced samples and messy storage shelves. Then, a new idea occurred to her. What if the physical samples were stored in a kind of library system, like the digital data? In this hypothetical system, researchers could pass the samples on to a data manager, who would then upload descriptions to a central database. Other researchers would request certain samples by submitting a digital form detailing which samples they need, what questions they would attempt to answer, and what data analyses they plan to do. Finally, the data manager would process the request and transfer the samples to the appropriate researcher. After they served their purpose, the samples would be re-shelved under that same system. A place for every sample, and every sample in its place!
As it turned out, Bev’s idea was not at all crazy, and it did work. She presented it to the directors, and they set aside funds to begin an inventory makeover. Today, they are working towards reinstating order with Bev’s developing library system and her organizational know-how.
The process has been long and slow, but those involved in carrying out the study recognize the complexity of the job at hand. Bev and her assistants are moving towards a better organization system, one box at a time.